Carbon fiber composites
Exploring the dynamic world of carbon fiber involves delving into advanced manufacturing techniques, high-performance applications, and versatile carbon fiber composites. From carbon fiber sheets to reinforced polymers, the technology behind carbon fiber continues to revolutionize industries, offering innovative products and showcasing its exceptional properties.
50%
Sports and RC
30%
Marine and Boat
20%
Others
How we help your business grow
Guarantee
Maximum value
Price
Competitive & Reasonable
Customization
Base on customer preferences
Quality
Never compromise
Delivery
Always on time
24
Quotation in HR
35
Production in DAYS
72
Express service in HR
25
Rush order deliver in DAYS
Carbon fiber
Technical data
Density: Lightweight at about 1.6 g/cm³.
Tensile Strength: Varies by grade, e.g., standard modulus around 300 ksi.
Modulus of Elasticity: Stiffness ranges from 15-50 Msi.
Thermal Conductivity: Low, around 1-10 W/m·K.
Electrical Conductivity: Conductive due to graphite structure.
Fatigue Resistance: Generally good, influenced by conditions.
Corrosion Resistance: Inherently corrosion-resistant.
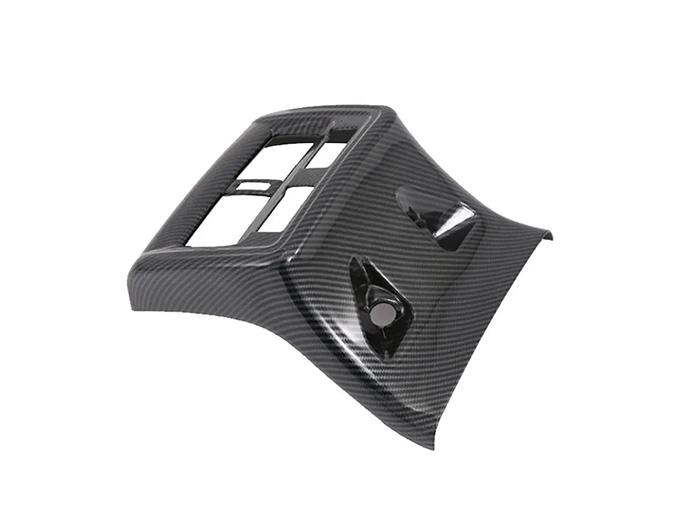
We do not just provide parts.
We provide answer and solution.
CNC milling of carbon fiber components
Carbon fiber CNC milling involves using CNC machines to precisely shape carbon fiber materials. Steps include design, material selection, machine setup, tool selection, generating tool paths, milling, cooling, finishing, and inspection. Skilled operators ensure accurate results and leverage carbon fiber's strength and lightweight properties. |
Forming process carbon fiber components |
Vacuum infusion is a process for making strong, lightweight carbon fiber parts. Dry carbon fiber fabric is laid in a mold, and a vacuum bag is sealed over it. Resin is introduced under vacuum, saturating the fabric evenly. After curing, a uniform and lightweight composite part is created. This method is used in industries like aerospace and automotive for its consistent results and ability to produce complex shapes. |
Our materials
Available materials
Standard Modulus (SM or T300): Balance of strength and stiffness.
Intermediate Modulus (IM or T700): Higher strength and stiffness, aerospace.
High Modulus (HM or T800): Exceptional stiffness, sports equipment.
Ultra High Modulus (UHM or T1000): Extreme stiffness, specialized uses. Pitch-Based: Heat resistance, industrial applications. Pan-Based: Common, balanced cost and performance. Spread Tow: Enhanced mechanical properties, high performance. Unidirectional: High strength along one axis. Woven Fabric: Various weaves, strength levels. Hybrid: Mixed with materials like Kevlar or fiberglass for specific traits. |
Briefly explained
How does vacuum forming and CNC milling carbon fiber work?
Vacuum Forming Carbon Fiber:
Carbon fiber fabric is laid on a mold.
Heat makes resin tacky.
Vacuum removes air, forming carbon fiber to mold.
Curing solidifies shape.
CNC Milling Carbon Fiber:
Digital model created.
Carbon fiber sheet secured.
CNC machine cuts based on programmed paths.
Specialized tools handle abrasive carbon fiber.
Finishing for desired surface.
Both methods create precise carbon fiber components for diverse applications.
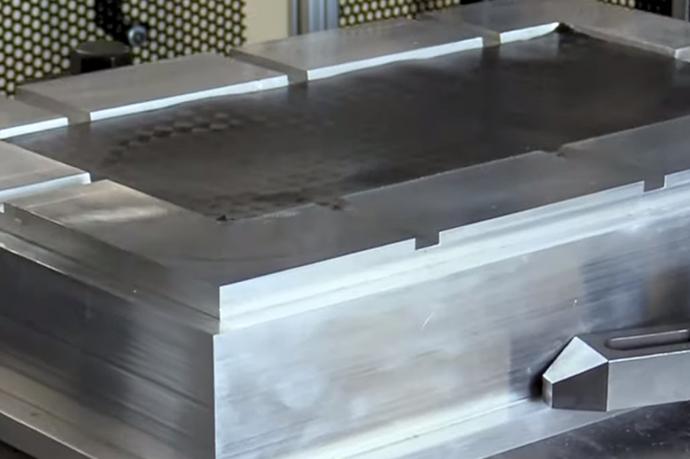
Surface treatment
We get the best out of your Carbon fiber components
Wax treatment involves applying wax to the surface of carbon fiber to achieve various benefits:
Protection: Wax forms a protective barrier against moisture, UV rays, and environmental factors, extending the material's lifespan.
Enhanced Appearance: Waxing imparts a glossy finish, enhancing the aesthetics of carbon fiber components.
Smooth Surface: Waxing can create a smoother texture, reducing drag and improving aerodynamics.
Water Repellency: Wax makes surfaces hydrophobic, causing water to bead and slide off, valuable in applications requiring water resistance.
Easy Cleaning: A waxed surface is easier to clean, as dirt and debris are less likely to adhere.
UV Resistance: Certain waxes contain UV inhibitors, shielding against fading and deterioration due to sunlight.
To ensure effective wax treatment, select a wax compatible with carbon fiber and follow proper application guidelines. The choice of wax and technique may vary based on the intended use of the carbon fiber part.
Your partner for all components
Other manufacturing processes
Sourcing easier than ever
Perfect components in 3 steps
1
Get a quote
Send manufacturing drawing and specify order. You will receive your quote within 48 hours.
2
Quality control
We find the right manufacturer, monitor production and take care of quality control
3
Receive components
You receive your quality-tested components including a detailed test certificate.
We go beyond being a supplier.
We are an extension of your success.
Hear from the real MVPs
Our Customers
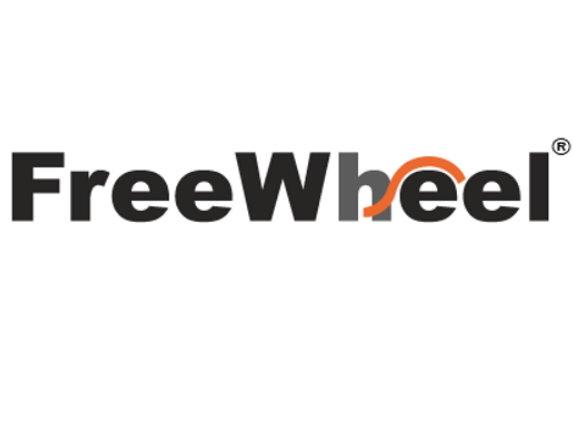
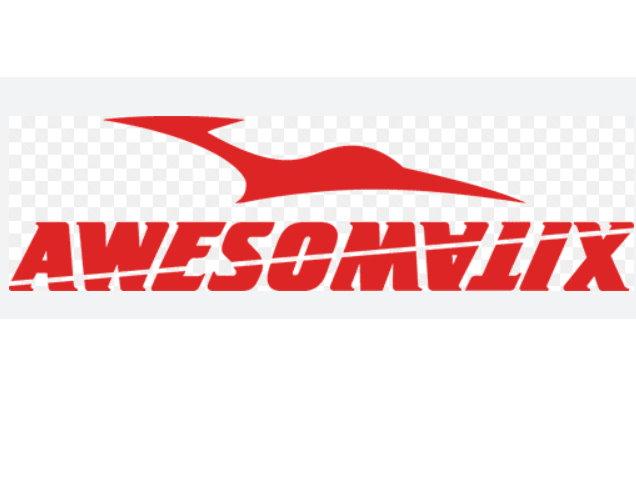
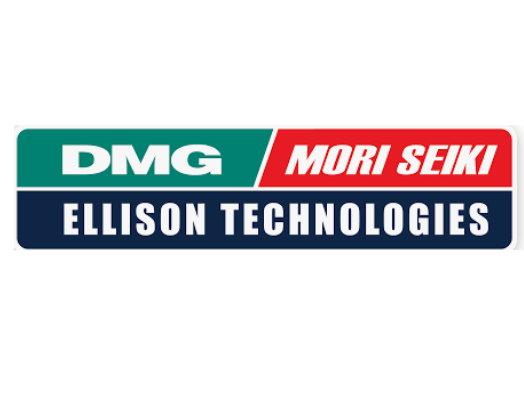
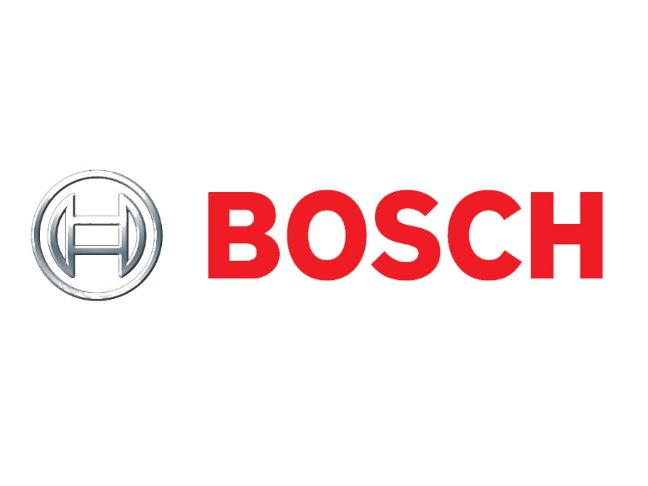
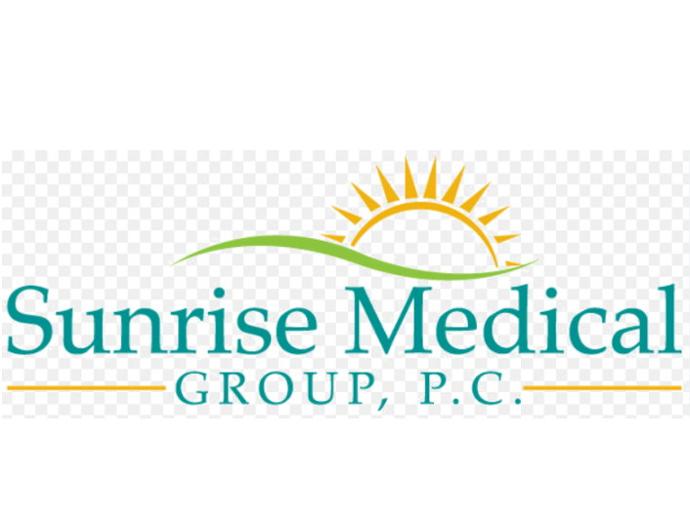
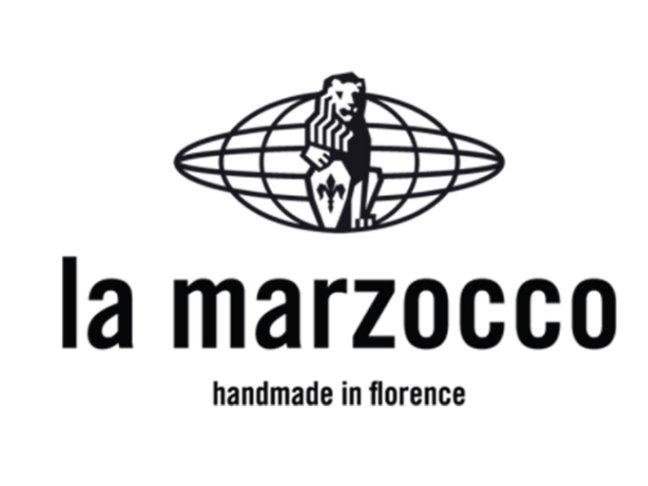
Tony Fred, Senior Buyer
Hi Jim,
We greatly appreciate the exceptional service provided by you, great good looking CNC parts, which has significantly contributed to the success of our research projects and enabled us to achieve breakthroughs in record time.
Mich Stark, R & D Engineer
Hi Alice,
Just want to say your outstanding service is super impressive. Your great job on our stainless steel bending case makes our espresso coffee grinder added value. It really makes it look nice, super well done.
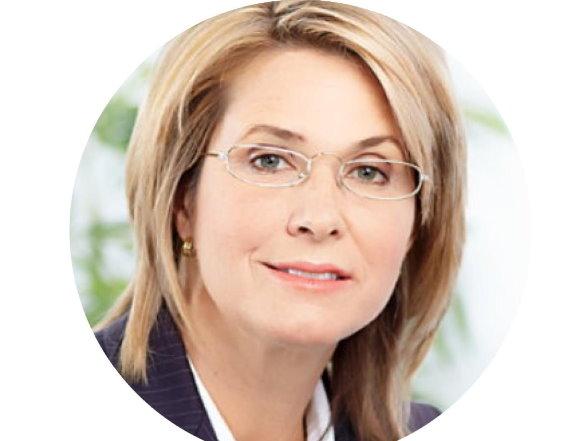
Aline Turner, SR procurement
Hi Alice,
We would like to say thank you to you Alice, DMS delivered our parts very fast with excellent quality that is what we are expecting, hopefully you will see our next order very soon, by the way Alice, please say hi to Jennifer for me.
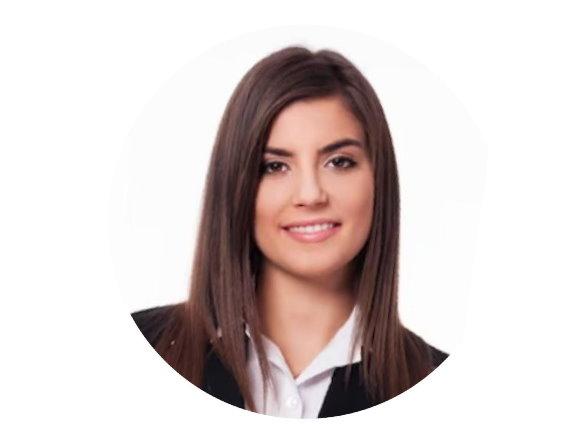
Iris Joe, Engineering Designer
Dear Alice,
Now I can say it is a right decision to move our production from China to DMS, you guys are awesome, all the marine pads looks shinny no scratch founded, it is 8% more expensive compare to China but quality talks, we will keep buying more items from you for sure.
We transform your ideas into reality .
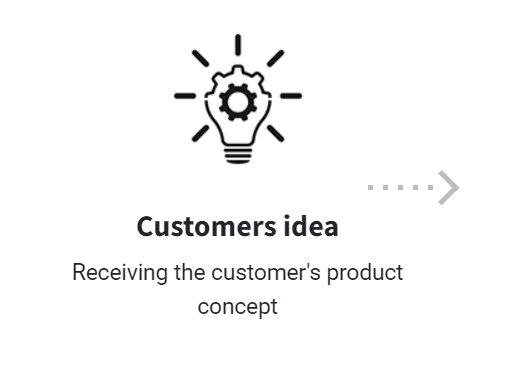
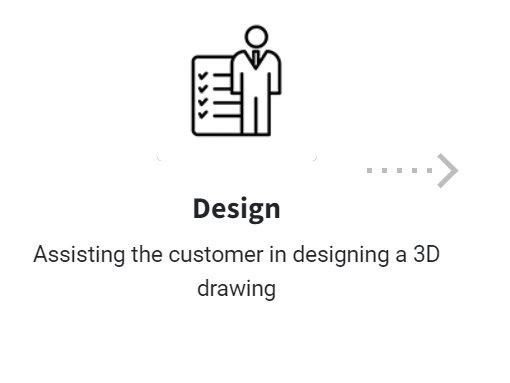
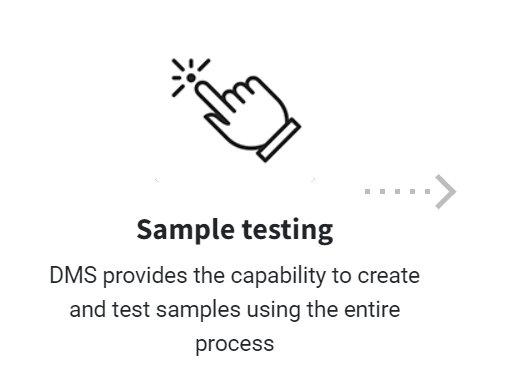
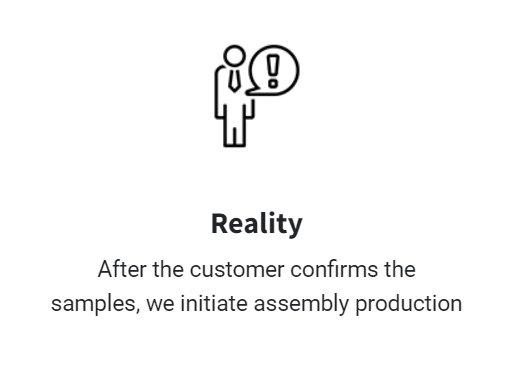