Aluminum die casting
The die casting industry utilizes advanced techniques and specialized machines for the precise production of aluminum and zinc die cast products, offering advantages such as high-pressure die casting, efficient processes, and innovative designs, making it a key player in manufacturing.
100%
Aluminum
How we help your business grow
Guarantee
Maximum value
Price
Competitive & Reasonable
Customization
Base on customer preferences
Quality
Never compromise
Delivery
Always on time
24
Quotation in HR
35
Production in DAYS
72
Express service in HR
25
Rush order deliver in DAYS
Simple processes for series production
Cost-effective series production in die casting
DMS specializes in high-efficiency and flexible series production and mass production through fully automated die casting. We work with a variety of metals, including aluminum, zinc, and magnesium alloys. Our state-of-the-art die casting processes ensure precise dimensions and tight tolerances. With both hot chamber and cold chamber techniques, we offer a range of surface finishing options. Count on DMS for streamlined die casting production and seamless supply chain management.
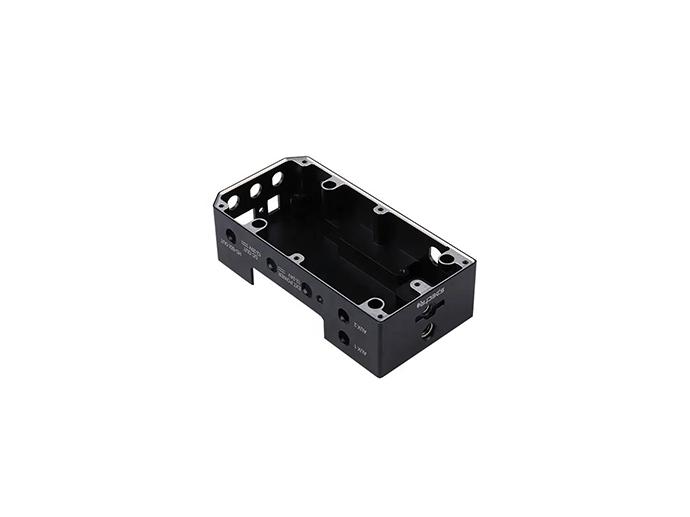
We do not just provide parts.
We provide answer and solution.
Die casting
Technical data
Material thickness: | 1 mm to 12 mm |
Casting size | 150mm x 150 mm x 150 mm |
Casting weight | from 1g to 15 kg |
Tolerances: | from 0.05 mm |
Closing force: | 80 – 2000 T |
Die casting tools: | Multiple cavities |
Ideal batch sizes: | from 1,000 piece |
Our materials
Available materials
Aluminum : A 380. A 383. A360. |
Brass |
Zinc |
Silicon Tombac |
Briefly explained
How does die casting manufacturing work?
Die casting is a manufacturing process where molten metal, typically aluminum, zinc, or magnesium, is injected under high pressure into a reusable mold. The metal cools and solidifies in the mold, creating precise, complex parts with excellent surface finish. Die casting is cost-effective for large production runs and offers design flexibility, but it has limitations for extremely large or intricate parts.
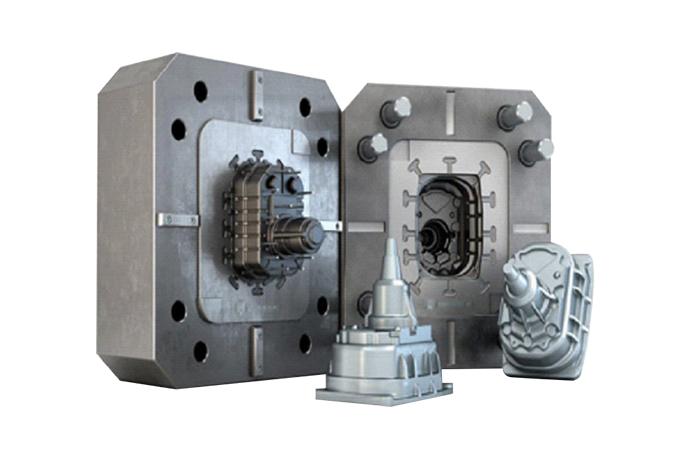
Zinc and Magnesium
Hot Chamber Process
The hot chamber process is the most widely used die casting process. In this process, the casting vessel is immersed directly in the molten metal. The molten metal is forced into the die through a swan-neck-shaped pouring nozzle. The hot chamber process is used for metals with a low melting point, such as zinc and magnesium alloys.
Aluminum
Cold Chamber Process
The cold chamber process is used for alloys with a higher melting point. In this case, the casting set is located outside the metallic melt. The material is fed from an external melt pot directly to the injection cover, where a hydraulic piston injects the metal into the mold. The cold chamber process is mainly used in aluminum die casting.
Surface treatment
We get the best out of your components
At DMS, we understand that refinement, appearance, and protection against wear and corrosion are essential aspects of our core business. We not only focus on the production of components but also prioritize the refinement and surface treatment of turned parts. Our expertise extends to providing solutions that enhance the aesthetics, durability, and functionality of the components we manufacture.
-
Sandblasting
-
Paint
-
Anodizing
-
Powder coating
-
Electroless nickel
-
Galvanizing
-
Passivate
-
Chromate
Your partner for all components
Other manufacturing processes
Sourcing easier than ever
Perfect components in 3 steps
1
Get a quote
Send manufacturing drawing and specify order. You will receive your quote within 48 hours.
2
Quality control
We find the right manufacturer, monitor production and take care of quality control
3
Receive components
You receive your quality-tested components including a detailed test certificate.
Custom metal parts fabrication experts.
Hear from the real MVPs
Our Customers
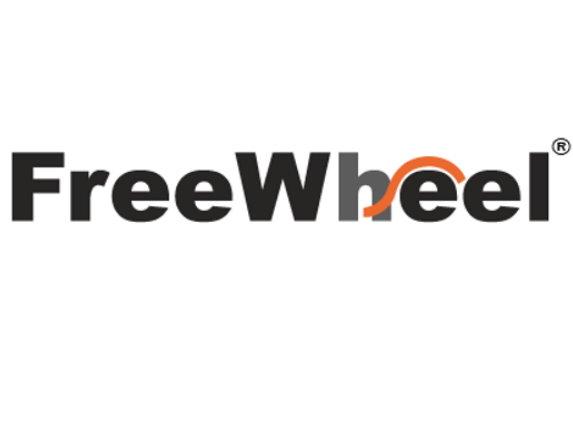
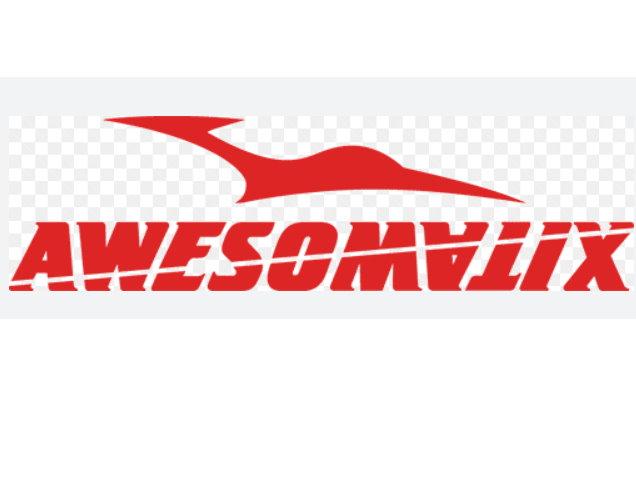
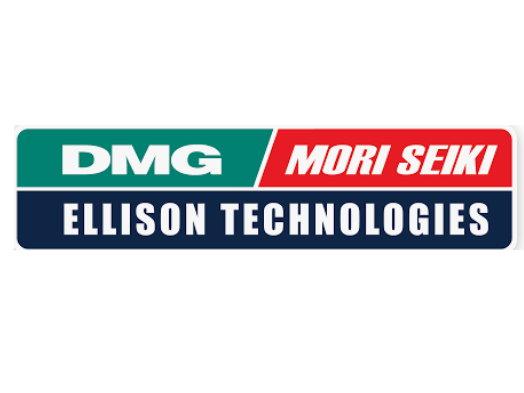
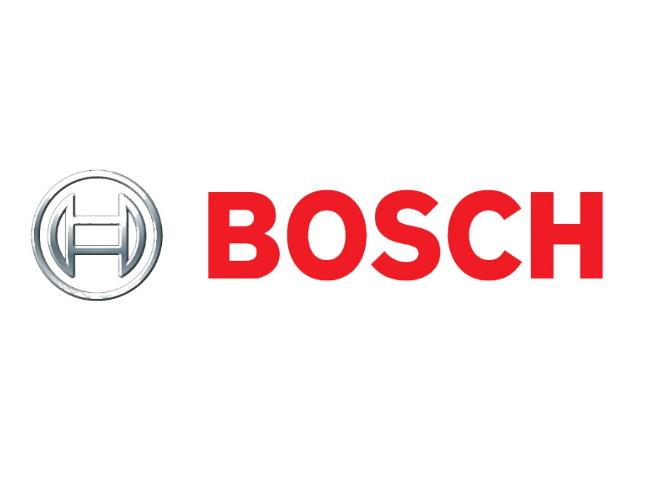
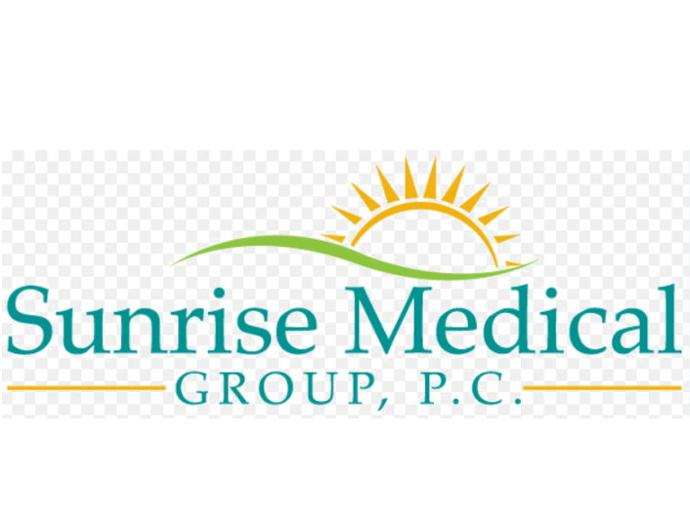
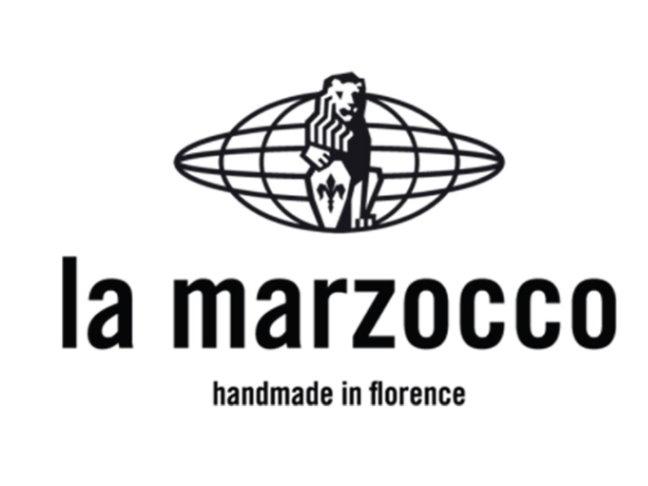
Tony Fred, Senior Buyer
Hi Jim,
We greatly appreciate the exceptional service provided by you, great good looking CNC parts, which has significantly contributed to the success of our research projects and enabled us to achieve breakthroughs in record time.
Mich Stark, R & D Engineer
Hi Alice,
Just want to say your outstanding service is super impressive. Your great job on our stainless steel bending case makes our espresso coffee grinder added value. It really makes it look nice, super well done.
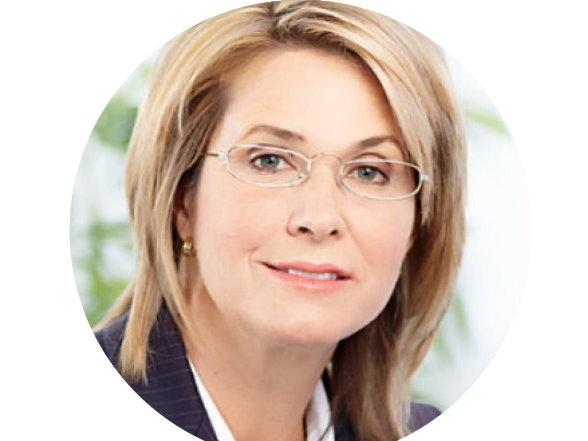
Aline Turner, SR procurement
Hi Alice,
We would like to say thank you to you Alice, DMS delivered our parts very fast with excellent quality that is what we are expecting, hopefully you will see our next order very soon, by the way Alice, please say hi to Jennifer for me.
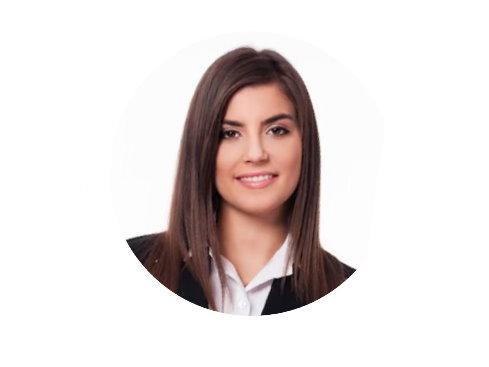
Iris Joe, Engineering Designer
Dear Alice,
Now I can say it is a right decision to move our production from China to DMS, you guys are awesome, all the marine pads looks shinny no scratch founded, it is 8% more expensive compare to China but quality talks, we will keep buying more items from you for sure.
We transform your ideas into reality.
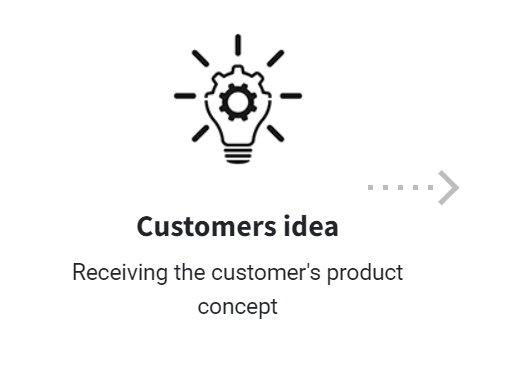
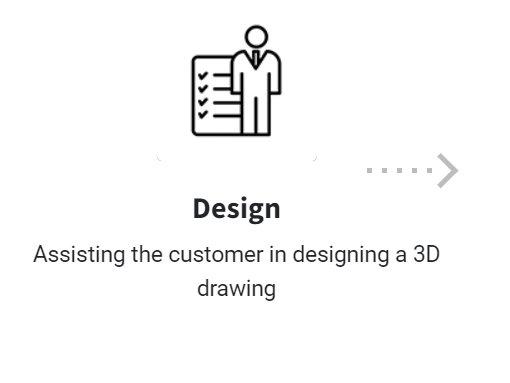
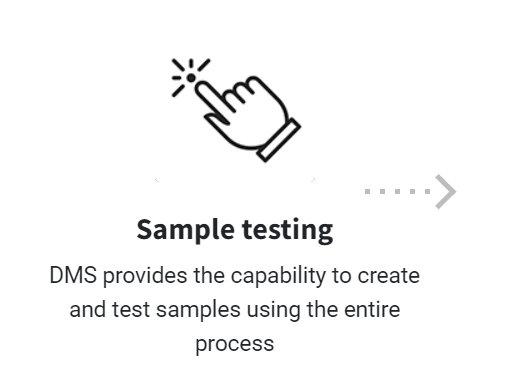
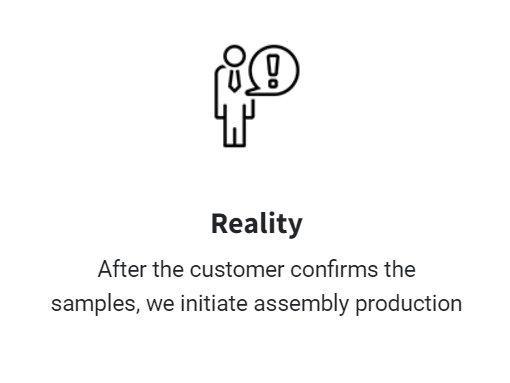